Structural Health Monitoring (SHM) is critical to maintaining the integrity and reliability of offshore megastructures during operation. Traditional visual inspections are labour-intensive, time-consuming, and often lead to operational downtime, posing challenges to the cost-efficiency and safety of these structures. Reliable, data-based SHM systems are essential to reduce downtimes and optimize inspection intervals. These systems enable operators to identify and address potential issues without relying solely on time-consuming inspections, ensuring the continuous operation of these megastructures.
A significant challenge in SHM is the handling of varying environmental and operational conditions (EOCs). Especially, offshore structures are exposed to various environmental influences, making it imperative to update simulation models to reflect these variations accurately and continuously. By combining prior knowledge (e.g., numerical models and digital twins) with data-driven approaches in a grey-box modelling framework, a more comprehensive mapping of the structural behaviour under varying EOCs can be achieved. This allows for reliable decision-making and robust SHM.
However, practical constraints add complexity. For large structures like offshore wind turbines, the limited number of sensor measurement points relative to the structure's degrees of freedom creates an inherent information deficit. Furthermore, deriving statistical models requires long-term data acquisition, which can be prohibitive in practice. Efficient utilization of available data and trained models is therefore paramount.
In this context, transfer learning emerges as a transformative approach. This machine learning technique allows models built on known data (source domain) to be adapted to new scenarios (target domain), even with unlabelled data. Transfer learning facilitates knowledge transfer across different structures by transforming damage-sensitive features into a common latent feature space, improving the SHM system's adaptability and reliability.
The subproject C02 aims to integrate the multivariate grey-box monitoring concept established in the first funding period with transfer learning methods developed during the second funding period. This integration enables a scalable and flexible SHM solution that applies to multiple offshore megastructures rather than focusing on individual structures. Additionally, incorporating numerical models, such as the digital twin from CRC 1463, into the database will enhance the system's capability to generalize across various structural scenarios.
The project's innovative approach lays the groundwork for population-based SHM (PBSHM) in the third funding period, aiming to monitor entire wind farms. By leveraging data and knowledge transfer, the research will create a foundation for efficient, reliable, and scalable SHM systems that support the sustainable operation of offshore megastructures.
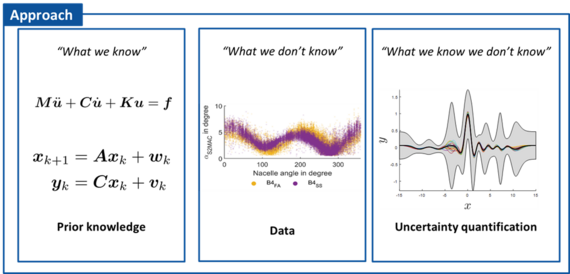
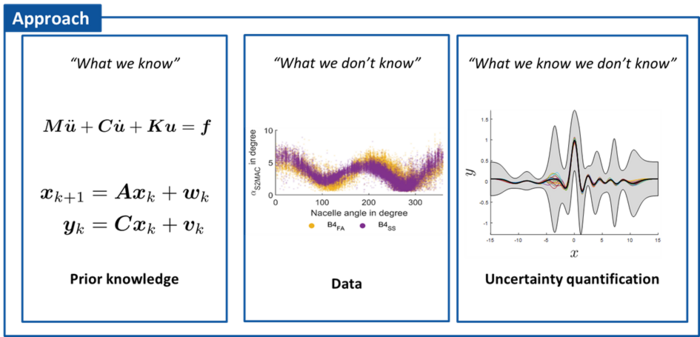
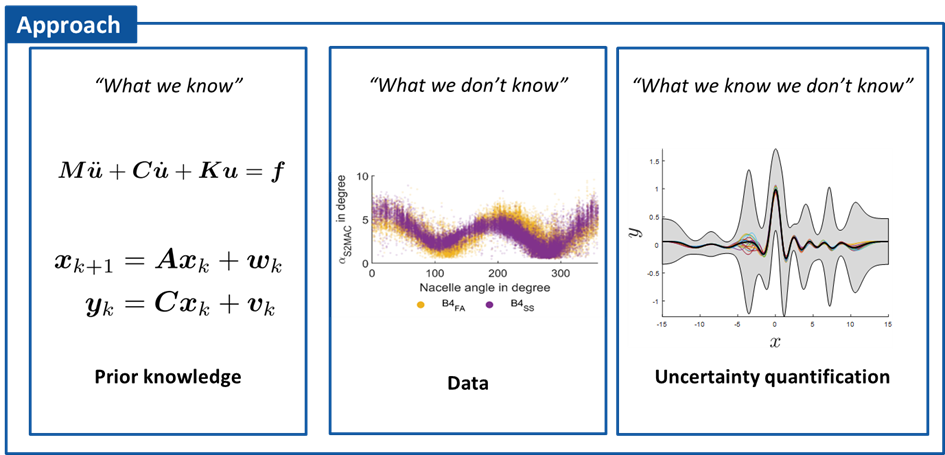
Results of the First Funding Period
The first funding period laid a strong foundation for advancing structural health monitoring (SHM) by combining robust operational modal analysis (OMA) algorithms (white-box methods) with machine learning techniques (black-box methods) into a multivariate grey-box structural monitoring framework. This innovative concept was tailored to monitor offshore megastructures under real operational conditions continuously. Key achievements include:
- Establishing the LUMO Benchmark Structure (Wernitz, 2022):
The Leibniz University Test Structure for Monitoring (LUMO) was set up as an open-access benchmark for SHM research. This structure provides a valuable database for testing and comparing SHM methods, fostering collaboration within the research community. - Development and Deployment of a Grey-Box Monitoring Concept (Möller, 2023):
A comprehensive grey-box SHM concept was developed and implemented based on the LUMO structure. This approach effectively integrated physics-based (white-box) and data-driven (black-box) methods, leveraging their strengths to enhance monitoring reliability and adaptability. - Application of Operational Modal Analysis to a Large Wind Turbine (Jonscher, 2024):
Methods from operational modal analysis were successfully applied to a fully operational 3.4 MW onshore wind turbine. This real-world application demonstrated the efficacy of advanced modal analysis methods in characterizing the dynamic behaviour of large-scale structures during operation. - Development of a Physically Motivated Heteroscedastic Gaussian Process (Jonscher, 2024):
A heteroscedastic Gaussian process model was developed to address the challenges of varying operational conditions. This physically inspired approach provided a robust framework for monitoring wind turbines, enabling the identification of damage-sensitive features despite environmental and operational variability.
These results highlight the successful integration of theoretical advancements and practical applications, establishing a robust methodology for monitoring offshore megastructures. The achievements of the first funding period provide a solid groundwork for extending the grey-box monitoring concept and addressing the challenges of multi-structure and population-based SHM in subsequent funding periods.
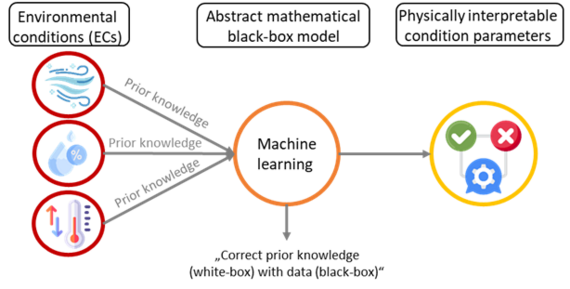
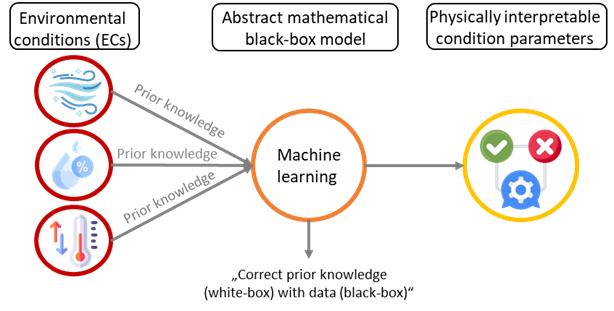
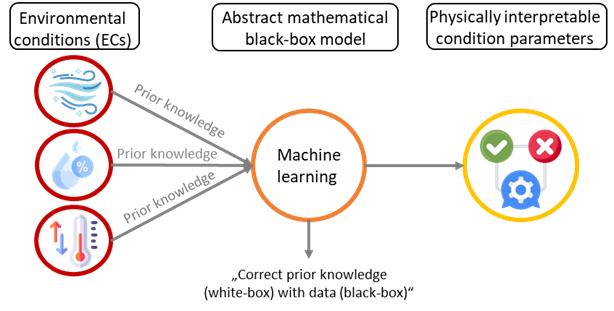
Objective and approaches for the second funding period
Building upon the foundational work of the first funding period, the second funding phase aims to significantly enhance the scalability and adaptability of Structural Health Monitoring (SHM) methods. The primary goal is to shift from monitoring individual structures to addressing multiple structures simultaneously, paving the way for population-based SHM. This expansion requires overcoming key challenges related to limited training data and computational efficiency. The objectives and approaches for this phase are as follows:
Objectives of the Second Funding Period
- Addressing Multiple Structures:
Develop methods that enable monitoring many structures rather than focusing solely on individual ones. This approach supports a broader application of SHM, such as within entire wind farms. - Mitigating Information Deficits:
Compensate for limited training data, such as incomplete coverage of environmental and operational conditions or the absence of labelled damage states. This ensures the robustness of SHM methods even when the data is sparse or incomplete. - Reducing Computational Costs:
Avoid time-consuming training phases by optimizing computational efficiency. This is crucial for deploying SHM systems in real-world scenarios with limited computational resources.
Approaches for the Second Funding Period
- Verification and Validation:
- Verification through the established LUMO benchmark structure ensures the reliability of the developed methods.
- Validation using real-world test cases, including the PreciWind research turbine, the German research wind farm WiValdi (DFWind), and the real-world lab 70 GW offshore wind. These diverse testbeds allow for rigorous testing under practical conditions.
- Knowledge Transfer Using Transfer Learning:
Leverage transfer learning to explore the transfer of knowledge between different structures. This technique reduces reliance on extensive labelled data and accelerates the adaptation of models to new scenarios. - Quantifying Structural Similarities via Graph Theory:
Apply graph theory to quantify the similarities between structures. This enables systematic investigation into the transferability of knowledge and the identification of shared features across structures. - Domain Adaptation (Unsupervised and Supervised):
Develop methods for domain adaptation, both unsupervised and supervised, to couple the techniques from the first and second funding periods. This coupling maximizes the fidelity of data-based SHM by adapting trained models to new environmental, operational, and structural contexts.
Through these objectives and approaches, subproject C2 aims to create a robust, efficient, and scalable SHM framework capable of handling diverse and complex structural scenarios, ultimately supporting the development of population-based SHM for large offshore wind farms.
Publications
-
2025: Comparing Gaussian process enhanced grey-box approaches to detect damage in unknown environmental conditions due to climate change
Möller, S., Jonscher, C., Grießmann, T., Rolfes, R. (2025): Comparing Gaussian process enhanced grey-box approaches to detect damage in unknown environmental conditions due to climate change, Structural Health Monitoring, 2025
-
2025: Dynamic displacement measurement of a wind turbine tower using accelerometers: tilt error compensation and validation
(Kopie 1)
Jonscher, C., Helming, P., Märtins, D., Fischer, A., Bonilla, D., Hofmeister, B., Grießmann, T., Rolfes, R. (2025): Dynamic displacement measurement of a wind turbine tower using accelerometers: tilt error compensation and validation, Wind Energ. Sci., 10, 193–205, 2025
-
2024: Identification uncertainties of bending modes of an offshore wind turbine for vibration-based monitoring
Jonscher, C.; Möller, S.; Liesecke; L.; Schuster, D.; Hofmeister, B.; Grießmann, T.; Rolfes, R. (2024) Identification uncertainties of beding models of an offshore wind turbine for vibraion-based monitoring, Structural Control and Health Monitoring
-
2024: Heteroscedastic Gaussian processes for data normalisation in probablistic novelty detection of a wind turbine
Jonscher, C.; Möller, S.; Liesecke, L.; Hofmeister, B.; Grießmann, T.; Rolfes, R. (2024): Heteroscedastic Gaussian processes for data normalisation in probablistic novelty detection of a wind turbine, Engineering Structures 305, 117786
-
2024: Damage localisation using disparate damage states via domain adaption
Wickramarachchi, C.; Gardner, P.; Pool, J.; Hübler, C.; Jonscher, C.; Rolfes, R. (2024): Damage localisation using disparate damage states via domain adaption, Data-Centric Engineering 5, e3
-
2023: Validation of an FE model updating procedure for damage assessment using a modular laboratory experiment with a reversible damage mechanism
Wolniak, Marlene; Hofmeister, Benedikt; Jonscher, Clemens; Fankhänel, Matthias; Loose, Ansgar; Hübler, Clemens; Rolfes, Raimund (2023)
Validation of an FE model updating procedure for damage assessment using a modular laboratory experiment with a reversible damage mechanism
Journal of Civil Structural Health Monitoring -
2023: Investigations towards physics-informed Gaussian process regression for the estimation of modal parameters of a lattice tower under environmental conditions
Möller, S., Jonscher, C., Grießmann, T., Rolfes, R. (2023): Investigations Towards Physics-Informed Gaussian Process Regression for the Estimation of Modal Parameters of a Lattice Tower Under Environmental Conditions, EVACES 2023, Lecture Notes in Civil Engineering, vol 433
-
2022: A new open‐database benchmark structure for vibration‐based Structural Health Monitoring
Wernitz, Stefan; Hofmeister, Benedikt; Jonscher, Clemens; Grießmann, Tanja; Rolfes, Raimund (2022)
A new open‐database benchmark structure for vibration‐based Structural Health Monitoring
Structural Control and Health Monitoring, 29 -
2022: On noise covariance estimation for Kalman filter-based damage localization
Wernitz, Stefan; Chatzi, Eleni; Hofmeister, Benedikt; Wolniak, Marlene; Shen, Wanzhou; Rolfes, Raimund (2022)
On noise covariance estimation for Kalman filter-based damage localization
Mechanical Systems and Signal Processing, 170 -
2021: Dataset: LUMO - Leibniz Universtity Test Structure for Monitoring
Stefan Wernitz, Benedikt Hofmeister, Clemens Jonscher, Tanja Grießmann, Raimund Rolfes (2021)
Dataset: LUMO - Leibniz Universtity Test Structure for Monitoring.
Subproject Management
30167 Hannover
Staff
30167 Hannover
30167 Hannover