Offshore wind turbines (OWTs) operate in demanding environments where continuous monitoring is essential to capture the effects of ageing, environmental conditions, and operational stresses. These factors can lead to structural changes over time, making accurate and reliable data critical for maintaining the safety and efficiency of these systems. However, the monitoring systems also age and degrade, resulting in data inaccuracies, reduced reliability, and challenges in distinguishing between sensor faults and actual structural issues.
This project focuses on the improvement of the long-term monitoring and management of OWTs. The goal is to ensure that the digital twin remains accurate and effective throughout the OWT lifespan by accounting for the ageing of both the structures and the monitoring systems of the sensor network design.
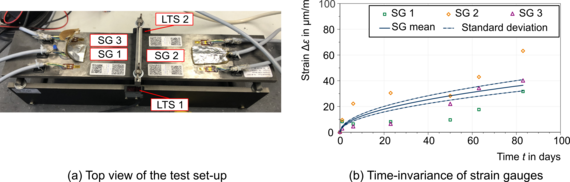
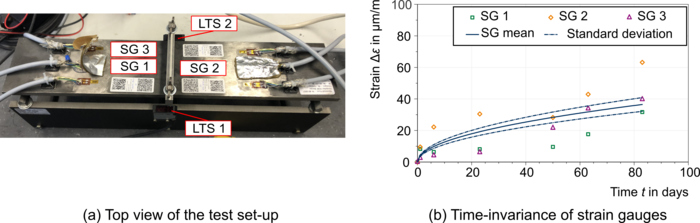
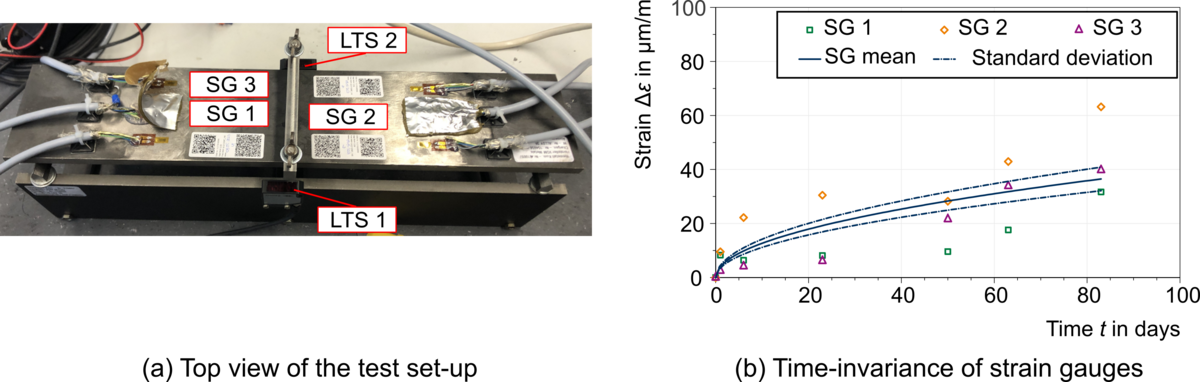
In the first phase, forward analyses were conducted to model the ageing behaviour of sensors, develop compensation measures, and establish a concept for optimally placed sensors, see Figure 1. The current phase shifts to inverse analyses, focusing on designing and validating reliability-based sensor networks that distinguish between sensor degradation and structural changes. This includes the development of a reliability-based optimal sensor placement algorithm, experimental validation on small- and large-scale structures, and using Bayesian inference to adapt sensor networks as they age.
The project is part of the Monitoring Cluster, working closely with related subprojects to enhance the connection between real-world OWTs and their digital twins. The results aim to improve monitoring systems, enable better decision-making, and support the efficient and reliable operation of wind farms.
Publications
-
2025: Addressing time variance in measurement systems with Bayesian model updating
Bartels, J.H.; Marx, S. (2025): Addressing time variance in measurement systems with Bayesian model updating; Sensors and Materials, 37(3), 921-942
https://fis.tu-dresden.de/portal/files/66785275/Bartels_2025_TimeVarianceMeasurementSystems.pdf
-
2024: Digital twins in wind energy: advancements in the life-time comprehensive digitization
Bartels, J.-H., Xu, R., Märtins, D., Schuster, D., Rolfes, R., Marx, S. (2024): Digital twins in wind energy: advancements in the life-time comprehensive digitization, 12 Sept. 2024, 15th European Conference on Product & Process Modelling (ECPPM 2024), Dresden, S. 1-8, 8 S.
-
2024: Datengestützter Assistent für den Entwurf von Offshore-Jacket-Substrukturen
Qian, H., Bartels, J., Peng, M., Marx, S. (2024): Datengestützter Assistent für den Entwurf von Offshore-Jacket-Substrukturen, Juli 2024, in: Bautechnik. 101, 11 S
-
2024: Conceptual design of offshore jacket substructures using machine learning
Qian, H., Bartels, J.-H., Marx, S. (2024): Conceptual design of offshore jacket substructures using machine learning, TORQUE 2024, 8 Aufl., Band 2767
https://iopscience.iop.org/article/10.1088/1742-6596/2767/8/082010
-
2024: Beschleunigungssensoren zur Zustandsüberwachung von Ingenieurbauwerken unter Einfluss von Umweltfaktoren bei tiefen Frequenzen
Bartels, J. H., Gündogdu B., Herrmann, R., Marx, S. (2024): Beschleunigungssensoren zur Zustandsüberwachung von Ingenieurbauwerken unter Einfluss von Umweltfaktoren bei tiefen Frequenzen. In: Bautechnik. 101, 10, S. 547-557
-
2024: Robust SHM: Redundancy approach with different sensor integration levels for long life monitoring systems
Bartels, J., Potthast, T., Möller, S., Grießmann, T., Rolfes, R., Beer, M., Marx, S. (2024): Robust SHM: Redundancy approach with different sensor integration levels for long life monitoring systems, Juni 2024, EWSHM 2024: 11th European Workshop on Structural Health Monitoring, NDT.net, S. 1-10, 10 S.
-
2024: Experimental Investigation on the Transfer Behavior and Environmental Influences of Low-Noise Integrated Electronic Piezoelectric Acceleration Sensors
Bartels, J., Xu, R., Kang, C., Herrmann, R., Marx, S. (2024): Experimental Investigation on the Transfer Behavior and Environmental Influences of Low-Noise Integrated Electronic Piezoelectric Acceleration Sensors, Feb. 2024, in: Metrology. 4, 1, S. 46-65, 20 S., 4
-
2023: Environmental influence on structural health monitoring systems
Bartels, J.-H., Kitahara, M., Marx, S., Beer, M. (2023)
Environmental influence on structural health monitoring systems; Life-Cycle of Structures and Infrastructure Systems: Proceedings of the Eigth International Symposium of Life-Cycle Civil Engineering (IALCCE 2023), 2-6 -
2023: Einflüsse auf die Messunsicherheit von SHM-Systemen und deren Kompensation am Beispiel von Laser-Distanzmessungen
Bartels, J.-H., Gebauer, D., Marx, S. (2023)
Einflüsse auf die Messunsicherheit von SHM-Systemen und deren Kompensation am Beispiel von Laser-Distanzmessungen, Bautechnikhttps://doi.org/10.1002/bate.202200102
-
2023: Robust SHM systems using Bayesian Model Updating
Bartels, J.-H., Potthast, T., Kitahara, M., Marx, S., Beer, M. (2023): Robust SHM systems using Bayesian Model Updating, Proceedings of the Thirty-third (2023) International Ocean and Polar Engineering Conference Ottawa, Canada, June 19-23, 2023
-
2023: Hardware redundancy for sensor degradation detection in SHM systems using strain gauge measurements
Bartels, J. H., Marx, S. (2023): Hardware Redundancy for Sensor Degradation Detection in SHM Systems using Strain Gauge Measurements, 19th EAWE PhD Seminar on Wind Energy, 6 - 8 September 2023, Hannover, Germany
-
2023: Bayesian updating with two-step parallel Bayesian optimization and quadrature
Kitahara, M., Dang, C., Beer, M. (2023): Bayesian updating with two-step parallel Bayesian optimization and quadrature, Computer Methods in Applied Mechanics and Engineering, 403, 115735
-
2022: Distribution-free stochastic model updating of dynamic systems with parameter dependencies
Kitahara, M.; Bi, S.; Broggi, M.; Beer, M. (2022): Distribution-free stochastic model updating of dynamic systems with parameter dependencies, Structural Safety 97, 102227
-
2022: Robust optimization of a dynamic Black-box system under severe uncertainty: A distribution-free framework
Lye, A., Kitahara, M., Broggi, M., Patelli, E. (2022): Robust optimization of a dynamic Black-box system under severe uncertainty: A distribution-free framework, Mechanical Systems and Signal Processing, 167, 108522
-
2022: Robuste, lebensdauerumfassende Monitoringkonzepte für Offshore-Windenergieanlagen
Bartels, J.-H. (2022): Robuste, lebensdauerumfassende Monitoringkonzepte für Offshore-Windenergieanlagen, 61. Forschungskolloquium des Deutschen Ausschusses für Stahlbeton (DAfStb) 26./27.09.2022 an der TU Dresden, 2022
-
2022: Measurement uncertainty in structural health monitoring systems for offshore wind turbines
Bartels, J.-H., Marx, S. (2022): Measurement uncertainty in structural health monitoring systems for offshore wind turbines, 18th EAWE PhD Seminar on Wind Energy, 2 - 4 November 2022, Bruges, Belgium
Subproject Management
30167 Hannover
Institut für Massivbau
August-Bebel-Straße 30/30A
01219 Dresden
Institut für Massivbau
August-Bebel-Straße 30/30A
01219 Dresden
Staff
30167 Hannover
George-Bähr-Str. 1
01069 Dresden
George-Bähr-Str. 1
01069 Dresden