Offshore megastructures require substructures with very large masses and dimensions due to their design and operating boundary conditions. Floating or shipping completely pre-assembled mega-substructures with heights of > 50 m, which are then firmly founded on the seabed, is very complex, logistically time consuming and allegedly inefficient. Modular mega-substructures are more suitable for offshore megastructures, cf. Figure 1, left.
By using extremely slim, thin-walled and resource-saving elements made of steel or high-performance concrete (HPC), weight-, mass- and transport-optimised modules can be prefabricated in a factory, which are then assembled offshore into mega-substructures. Modular mega-substructures combine the advantages of quality-assured and weather-independent prefabrication of modules by means of automated series production in the factory, highly consistent quality and shortened construction times with the advantages of easier transportability and reduced crane capacities offshore.
Central to the economic and ecological design as well as to the load-bearing capacity of these modular mega-substructures are simple, fast and durable joining methods for offshore installation. Conventional joining methods used in the offshore industry, such as welding-, grout and bolted joints, are time-consuming and cost-intensive to manufacture, dependent on metocean conditions in offshore environments and, in some cases, highly variable in their finished quality. An innovative alternative to conventional joints is so-called slip joints (Figure 1). Slip joints are push-fit connections between two pipes that transmit bending moments and axial compressive forces via friction. These slip joints can be designed both above and below the water level, do not require welding, grouting, or bolting of the pipe segments, and are virtually maintenance free. This innovative joining technology has already been successfully used for monopile substructures that are predominantly subjected to bending loads (Borssele V wind farm). In contrast to monopile substructures, where the slip joint is always overloaded by the dead weight of the tower and turbine (Figure 1, right), the alternating loads resulting from wind, waves and turbine operation in jacket substructures are predominantly introduced into the legs as axial force pairs and thus the slip joint connections are subjected to compression or tension (Figure 1, centre).
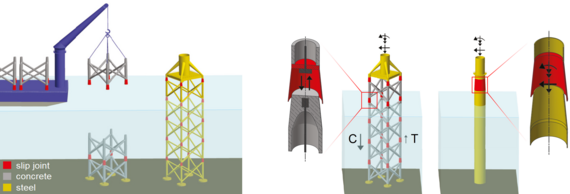
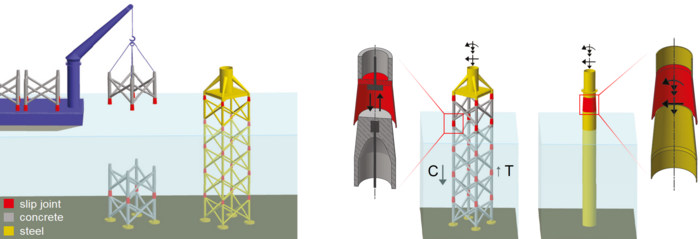
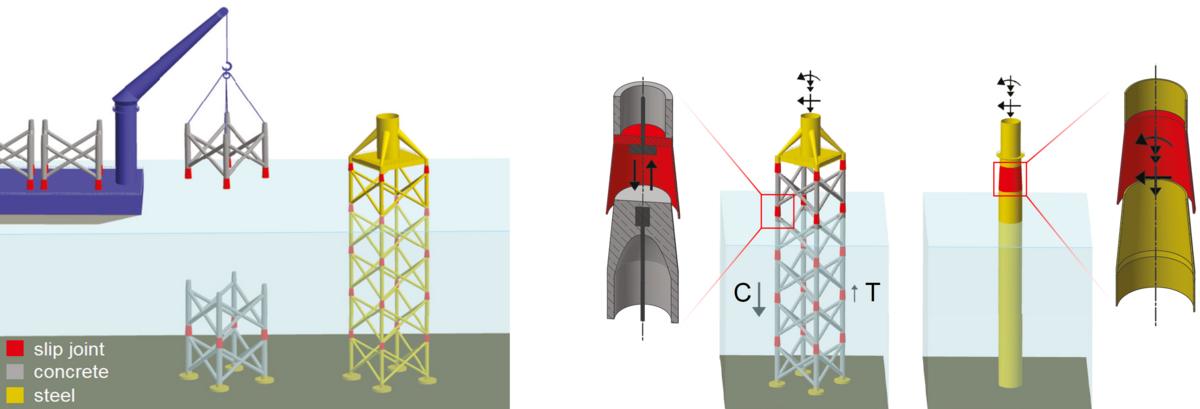
The goal of this subproject is to expand the design space of offshore megastructures to include modular substructure concepts assembled from modules using innovative slip joints. In addition to steel, the combination of steel and concrete will be investigated to develop even more durable as well as economical and ecologically sustainable mega-substructures. Here, the working hypothesis is that innovative pipe connections with slip joints have a high load-bearing capacity and enable easier, faster and almost weather-independent assembly of the modular mega-substructures at the installation site, resulting in durable, economical and ecologically sustainable offshore megastructures.
To verify the hypothesis, the joining process as well as the load-bearing and deformation behaviour of slip joints with steel-steel and steel-concrete contact surfaces under compression and, above all, tensile loads must be fundamentally recorded, analysed and described. In addition to numerical simulations, experimental joining tests, also under realistic marine environmental conditions with waves and currents in collaboration with A06, as well as compression and tension tests on steel-steel and steel-concrete slip joints will be carried out and documented, evaluated and analysed by means of mechanical measuring procedures and imaging methods. The results will be used to derive a mechanically based model for describing the compression and tension behaviour of slip joints with steel-steel and steel-concrete contact surfaces and, finally, to develop and numerically investigate modular substructure concepts. The main innovation of the subproject is the development of innovative slip joint connections that are capable of transferring high axial compressive loads and, above all, high axial tensile loads, thus enabling modular mega-substructures and significantly expanding the design space for offshore megastructures.
Subproject Management
Universitätsplatz 2
38106 Braunschweig
Universitätsplatz 2
38106 Braunschweig