Dynamic stall introduces transient loads that excite rotor blade vibrations. These vibrations contribute to mechanical fatigue and might lead to rotor failure. Predicting these loads and their impact on the aeroelastic stability of the rotor blade is crucial for designing future wind turbines. During the first funding period, subproject A2 validated a high-fidelity CFD model for predicting dynamic stall on wind energy megastructures, conducted a parameter study to investigate the sensitivity of basic aerofoil and flow parameters on dynamic stall and developed a reduced-order model (ROM) for predicting the onset of dynamic stall and the thus caused transient loads on large wind turbines. This model will be referred to as the initial ROM. The parameter study focused on dynamic stall induced by torsional modes of the blade and a steady inflow velocity.

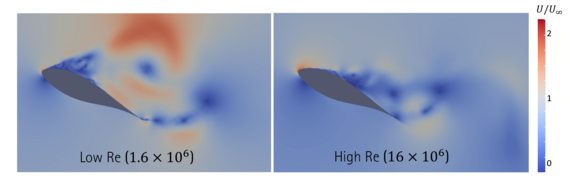
The goal of the second funding period is to improve and validate the initial ROM under more realistic operating conditions by accounting for superposed torsional and bending modes together with unsteady wind fields. This new approach will be carried out in two steps. These models enhance the prediction of dynamic loads acting on rotor blades of offshore megastructures during the design process and increase the reliability and accuracy of the load prediction. The final ROM will be able to simulate the influence of different aerofoil design and flow parameters on dynamic stall under realistic operating conditions, which in combination with the low computational effort allows for a cost-effective aerodynamic design of rotor blades such that they are less prone to aeroelastic failure and fatigue. In order to take realistic wind fields into account, large-scale eddies have to be prescribed at the inlet, which break up into smaller eddies downstream. This cannot be captured by eddy-viscosity based turbulence models, previously used in Unsteady Reynolds-averaged Navier-Stokes simulations (URANS).
The working hypothesis is that at very high Reynolds numbers, scale-resolving simulations (SRS) are able to predict dynamic stall induced by realistic blade motions and unsteady wind fields on wind turbine megastructures. Superposed torsion and bending motions of the blade (delivery from SP B03) and unsteady wind fields (delivery from SP A01 & SP A07) will be applied in both high-fidelity (SRS) and mid-fidelity (ROM) simulations. Derived insights are then to be included in the ROM by introducing new input variables, which enhance the prediction of dynamic stall induced by realistic operating conditions. The main methodological innovation of this subproject is an enhanced and comprehensively validated ROM, which predicts the transient loads under realistic operating conditions. During the first funding period, experiments concerning dynamic stall with a maximum Reynolds number of 0.35 M were used for the validation of the CFD setup. The recently published experimental results by Kiefer et al. (2022), regarding transient dynamic loads with a maximum Reynolds number of 5.5 M, will be used for the validation of the high-fidelity CFD simulations during the second funding period.
The subproject is part of the project area A, design boundary conditions, in which it analyses realistic blade deformations, unsteady wind fields, and turbine wakes with high-fidelity CFD simulations to ensure aeroelastic stability of the rotor blades. Critical inflow conditions and blade deformation that can lead to dynamic stall are identified, assessed, and shared with subprojects A01, B03 and Z01 to ensure a holistic design of the digital twin (DT). The dynamic stall models will be directly integrated into the DT during this funding period.
Publications
- 2025: Characterization of dynamic stall of a wind turbine airfoil with a high Reynolds number
- 2023: Computational Fluid-Structure Interaction towards Simulating Large Wind Turbines with openFOAM and deal.II Coupled via preCICE
- 2022: A novel and costeffective approach to simulating dynamic stall on rotating wind turbine blades with a changing angle of attack
- 2021: Transitional DDES study over a circular cylinder and an airfoil profile
Subproject Management
30823 Garbsen
Staff
30823 Garbsen